Advantages of MES for manufacturing
Benefits, functions and scope of a Manufacturing Execution System (MES)
Overview: MES advantages for manufacturing companies
"What is MES"? We like to answer this question as follows: Manufacturing Execution Systems (MES) are central information hubs as well as control and monitoring systems in manufacturing. A MES enforces planning and production specifications and transmits feedback on the production process in real time. It plays a significant role in managing the increasing complexity and the associated cost pressure in manufacturing. It creates more transparency, comprehensive traceability and documentation, and it provides important data for the further improvement of production processes.
For us, an MES stands at the centre of every successful digitalization strategy of manufacturing companies. Together with our customers, we have been successfully implementing Smart Manufacturing solutions for Closed Loop Manufacturing based on a powerful, scalable and future-proof MES/MOM solution platform for 20 years.
Our MES expertise
We succesfully implement MES solutions in various industries worldwide for 20 years.
What are the benefits of an MES?
A Manufacturing Execution System monitors, controls and optimizes manufacturing processes. Industry-specific MES functions and professional implementation lead to improved productivity, quality, compliance and cost efficiency of manufacturing processes and enable a fast ROI.
Benefit dimensions of an MES:
- Time
- Costs
- Quality
- Strategy
- Compliance
- Quality assurance
- Risk hedging
Reduced time spent
-
Reduced lead time, for example through improved OEE and paperless process control
-
Faster new product implementation (NPI), for example through the digital twin of the product and digital models
-
Less time spent on regulatory compliance, for example through process reliability and traceability
Reduced costs of production
-
Lower manufacturing costs through improved OEE and paperless process control, for example
-
Lower process costs through reduced effort and elimination of paper processes and redundant data
-
Lower inventory costs through reduced safety stocks
Higher quality in manufacturing
-
Reduced risk of documentation and process mistakes
-
Reduced efforts for non-conformances, for example through automatic data collection and analysis
Strategy for production control
-
Platform and product standardization and their modularization
-
Digital twin of product & production
-
Standardization and harmonization of processes
-
Control of complexity in closed loops
-
Decisions based on real data and KPIs
Ensuring compliance
-
Full traceability
-
Validated approvals/specifications - compliant with 21 CFR Part 11
-
Automated eDHR
-
Process reliability regarding the 5 M's (material, man, machine, method and measure)
Ensuring quality
-
Single source of truth for manufacturing and quality data
-
Automated data collection and analysis
-
Statistical methods (SPC, AQL, ...)
-
Configuration, variant and change management
Strategic risk management
-
Intrinsic compliance with regulatory processes
-
Process validation and conformity
-
Real-time alarms
-
Central Analytics & Reports

Schedule a 15 min appointment
You have read enough and would like to talk to us directly?
Selection of successful MES customers




What advantages does MES offer?
A modern, future-proof MES solution platform offers multifunctional features for optimizing your manufacturing processes.
Intelligent data acquisition and collection makes the status of manufacturing available in real-time while archiving all operational processes
Continuous assurance of manufacturing specifications by the system, traceability of production regarding orders, materials, resources, etc.
Optimally executed manufacturing plans lead to shorter cycle times, on-time deliveries and reduced demands on limited resources
Direct access to manufacturing documents and management of forms such as work instructions
Maintenance and consideration of competences or certifications of employees increases occupational safety and manufacturing quality
Tracking resource usage based on time of use and time of production, ensuring the compliance with maintenance requirements
Management and tracking of movements and storage of materials, intermediate products and finished products
Optimization of the manufacturing (order based on prioritization and rules) under consideration of material and resource availability
Up-to-the-minute reports on current manufacturing processes, including OEE data for resource usage, availability, cycle times and order fulfillment
Monitoring of manufacturing processes with decision support for users to correct and improve process steps and functions
Consistent consideration of quality standards and limits through preventive measures and event management to ensure high product quality
Central management of production-relevant resources such as machines, tools, employee skills, materials, processes, etc.
MES considers 5M process requirements of quality management
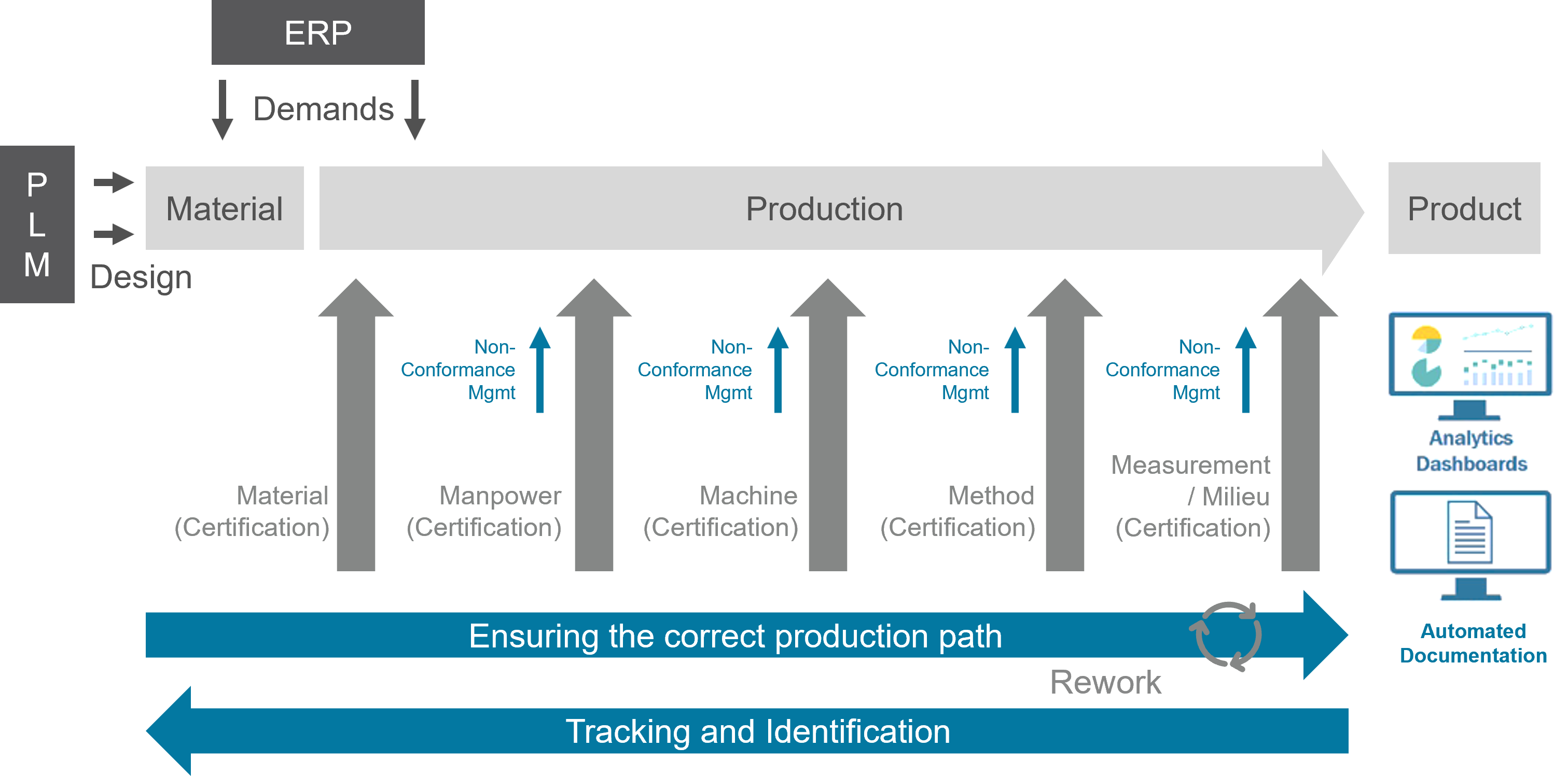
Our MES industry expertise
More expertise through a professional partner network
If your requirements demand it, we use our efficient partner network to ensure the best possible complete package for you.




Complete integration of the shop floor
The seamless integration of machines and sensors on the shop floor is a success factor for the efficient use of a Manufacturing Execution System. The availability of all information creates maximum transparency and enables the automated implementation of manufacturing specifications. The PAC (Process Automation Controller) solution developed by ZNT is a powerful, open platform for your equipment integration and automation in the manufacturing industry. PAC integrates your entire shop floor with the MES and other higher-level systems and offers central and uninterrupted administration with flexible options for deployment.

What successful MES customers say
“Through a reduction of DHR review time by 75 percent we were able to adjust resources and increase our NPI significantly.”
“We were able to reduce our non-conformances by 80 percent within the first two months of the Opcenter EX MDD implementation, eliminate all documentation errors and reduce the number of NCRs close to zero."
“By using Opcenter EX MDD as central digitilization platform we reduced our scrap by 95 percent and achieved a significant cost reduction."
Schedule your personal appointment for a short presentation:
You can choose between 15 and 30 minutes for your first appointment.
When booking your appointment, please tell us briefly your three most important requirements so that we can prepare individually.